EXPERIENCED & FRIENDLY LONDON PLUMBERS
Need an effective and efficient London plumber to visit your property? Get your free and transparent quote now. No hidden fees and no obligation to go ahead.
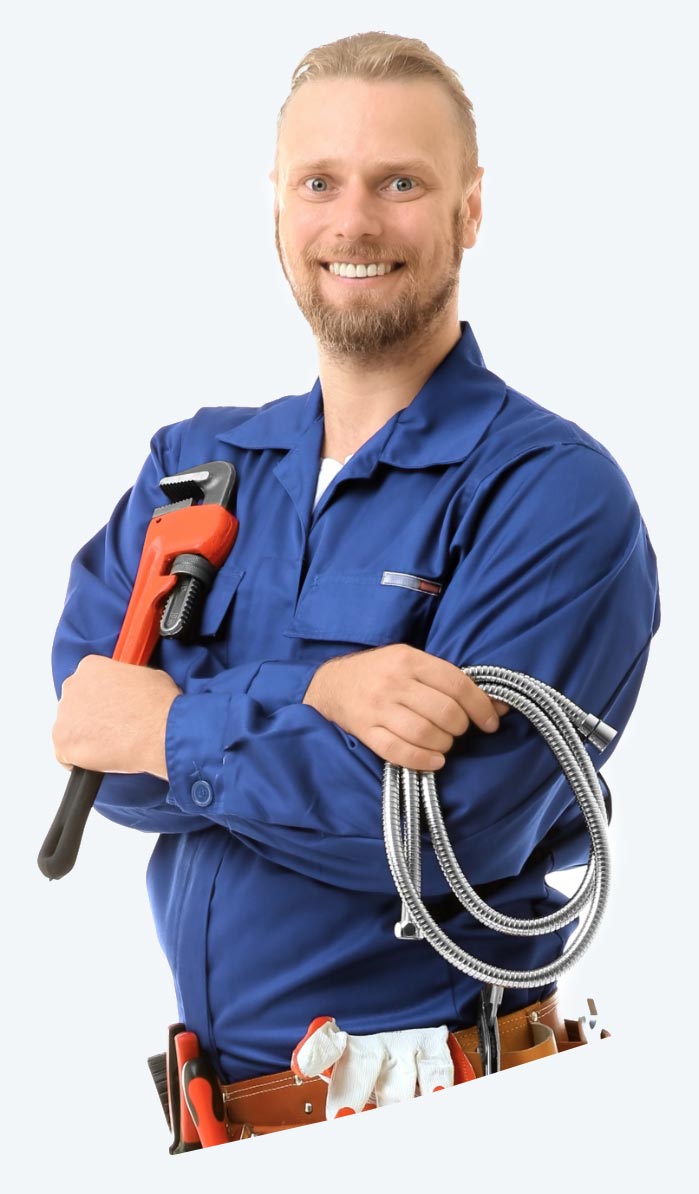
We are a team of versatile and fully trained plumbing specialists always on hand to help you. There is no plumbing need we can’t meet. Check out some of our most popular plumbing services below:
We are on hand for every burst pipe, clogged drain or leak, with our 24/7 emergency call-out appointments.
From faulty taps to odorous drains, our team is available for all of your general plumbing needs and ongoing maintenance work.
Our specialist team are trained to identify and repair leaks quickly and effectively, minimising any water damage as fast as possible.
The average leaky tap can waste 90 litre of water a week, we will fix yours as part of our affordable tap repair and replacement service.
Our quick and simple toilet installation and repair service will leave your facilities ready to use in no time.
Experienced in sink, toilet, drain and pipe blockages, there is no blockage we can’t fix.
Your employees safety matters, so book a comprehensive commercial plumber today and keep your office and staff safe.
Our experts will get your heating back on and your hot water running again, so you can carry on with your day.
Whether you have a combi, system or conventional boiler, we can install it safely, with minimal disruption.
Our friendly customer service advisors are ready to receive your call and provide you with a free, fixed and transparent quote for the work you need done.
We guarantee that we will meet your individual needs, whether that means working flexibly to fit you in for an emergency appointment, or understanding your unique requirements and following the processes most suitable for your situation.
Where specific certification is required for a job, we will be more than happy to provide you with details and proof of our accreditations and certifications.
Get your free and transparent quote, or call us now on 0203 519 6605.
Our team is punctual, professional and mindful when they attend your property.
We will bring all the necessary equipment and crack on to get the job done as efficiently and safely as possible, enabling you to get back to your daily routine.
We will never leave you waiting around, nor will we expect you to lift a finger.
It’s no secret that plumbing repairs and emergencies can be messy, with burst pipes and smelly blockages being the most common culprits.
However, our team promises to leave your property in a clear, clean, orderly and functioning fashion – something that our existing clients love to praise us for!
Before we leave, we will explain the work we have done, what changes we have made, how you can avoid future problems and how to get in touch with us again if you need any further support.
We are here for our clients as and when they need us, even after we finish a job.
Contact us for check ups, maintenance and general enquiries.
We build long-lasting relationships with our clients, delivering reliable services and maintaining high levels of customer satisfaction.
So, it’s no surprise so many clients return to us for their other plumbing, installation and repair projects.
Plumbing emergencies can happen at any hour, so our services are available at all hours.
We are open 24 hours a day, 7 days a week – so you will never be left in the lurch.
We never cut costs, especially when it comes to the parts we use in our services.
We use parts that are approved by the Water Regulations Advisory Scheme, so you know you are always getting the best when you hire us.
Health and safety are paramount in our line of work, which is why certification is crucial.
We are fully certified. When you book with us you will have peace of mind knowing that only accredited experts are working on your property.
We are proud to share our certifications with you and you can ask for further proof of our credentials at any stage of the process.
Too often we hear horror stories where plumbing companies have oversold unnecessarily to customers or under delivered massively to cut costs.
We take our reputation seriously and vow to do neither.
We are renowned around London for our integrity, honesty and fairness. Our customers continued use of our services is proof of this.
We perform our services to a high quality, but maintain efficiency in everything we do.
We act quickly where it is needed, such as for leaks resulting in water damage, but we also act carefully to ensure all safe and proper procedures are met.
London can be expensive, but hiring a plumber doesn’t have to be.
We offer affordable pricing across all of our services, and pride ourselves on our free and no-obligation quotes.
Our plumbers are Gas Safe registered.
This means that we are qualified to provide you with gas and heating services alongside our standard plumbing work.
Often a plumber won’t know the exact issue until they arrive at your property.
The last thing you want is to be stuck with a plumbing issue for an additional 2 hours because the visiting plumber isn’t qualified to work with gas appliances.
Calling a gas safe registered contractor ensures you’re not left in this uncomfortable position.
We are incredibly proud of the level of training, accreditation and certification our team holds.
These certifications prove our credibility and give our customers the confidence that they need to feel relaxed and calm in a plumbing emergency.
We deliver our services all throughout London and Greater London, covering every corner of the capital at all hours.
Our services are tailored to a broad range of properties, from commercial properties to your family home.
This means that we will be able to help you no matter your property size, type or location.
NORTH LONDON
NORTH WEST LONDON
WEST LONDON
SOUTH WEST LONDON
SOUTH EAST LONDON
EAST LONDON
CENTRAL LONDON
BROMLEY KINGSTON UPON THAMES
UXBRIDGE
HOUNSLOW
ILFORD
CROYDON
ENFIELD
HARROW
WATFORD
HILLINGDON
ROMFORD
Think you’ve got what it takes to be a UKOOA Plumber?
We are looking for experienced, enthusiastic and qualified professionals to join our UKOOA family, serving properties throughout London and Greater London.
Our team are the best in the industry, and we offer ongoing training and accreditation to keep it that way.
If you want to add to your experience and expertise with UKOOA, contact us.